Toscotec adapts to the changing landscape
TOSCOTEC ADAPTS TO THE CHANGING LANDSCAPE
Tissue making technology from different suppliers has merged to an extent in the past decade, so how do distinguish yourself in the field? Davide Mainardi explains Toscotec's process-based approach to this challenge
by Davide Mainardi - Sales & Customer Care Director, Toscotec S.p.A.
Until the Kimberly-Clark crescent former patent expired, several formation options for tissue machines vied for attention. But the crescent former was always the gold standard, and the industry has not looked back since it became generally available. There are important differences between wet end designs, but most tissue machine suppliers can produce a fast crescent former tissue machine based on the same formation principle. At Toscotec we would of course argue that our pioneering of, and expertise in, the steel yankee dryer sets us apart. We have proved the advantages of energy saving, safety, downtime reduction and product quality for 10 years since we installed the first steel yankee dryer. The enhanced thermal transfer is the most widely recognized advantage of the steel yankee dryer, but it offers other key benefits, such as the fact that more of its surface can be grooved compared with a cast-iron alternative, meaning a wider sheet for the same cylinder width. The superior hardness and homogeneity of the steel surface results in better creping efficiency and productivity, with reduced coating consumption thanks to the lower porosity of the surface. The steel yankee is also some 30 percent lighter than its cast-iron equivalent, which keeps down transport and civil works costs. It equates to a smaller carbon footprint for installation and operation.
Other tissue machine producers are starting to offer their own steel Yankees. We can claim market-leading experience and expertise in the technology, but it is another example of tissue-making technology from different suppliers coming up different sides of the mountain to meet at the same peak. Through-air drying (TAD) is another example of a technology which several suppliers have now mastered, including ourselves. A wide, 2,000 mpm tissue machine is now the standard, rather than the exception. So where do we go from here? Tissue making technology is not like converting, where innovations come thick and fast. We are all looking for that essential difference, but evolution rather than revolution has been the pattern. Where a quiet revolution is taking place, however, is in the role of the tissue machine builder.
The hub, but not the whole.
The tissue machine is the hub of our projects today, rather than the whole. Increasingly, customers seek a turnkey supplier, with expertise in all aspects of the mill. We are no longer a mechanical workshop, but a process supplier, responsible for all aspects of production including the critical factors of energy and minimizing fibre loss as well as chemical and water use. From multinationals to family-owned independents, different challenges require a flexible approach, rather than one-size-fits-all.
From a single component rebuild to a complete greenfield site - all require a specific approach and skills. From our "Modulo" (one of which we have just started up in Mediterranean Paper Mill in Syria) up to advanced "Ahead" lines, including TAD Vision we are handling capacities from 35 to 240 tpd, and this flexibility in output and technology is essential when dealing with the diverse needs of tissue producers across the globe.
In Europe, where greenfield projects are rare, you are likely to be working within an existing building, adapting and extending the services and support technology as necessary. If the replacement of an existing line is called for, we need to keep the paper-to-paper gap wafer thin while accounting for critical parameters such as the change in dynamic load which a new, faster tissue machine imposes on the infrastructure.
A German process challenge at SCA Hygiene involved a new tissue machine specified to use both slush pulp and dry pulp. The tissue machine was certainly noteworthy - a 220 tpd toilet paper unit with dilution consistency profiling, and automatic reeling with nip control. But the stock preparation was the special case. It is unusual for a mill to produce its own virgin fibre pulp in Europe, so this project required tissue machine dewatering capacity and the ability of the headbox to optimize consistency to keep energy consumption in check and provide the best sheet formation. This requires specific expertise. With global scope, however, the ability to work with slush pulp is a big advantage, with mills in India and China increasingly favouring integrated pulp and tissue production. It has also proved critical to us for Syassky Pulp & Paper in Russia.
Accommodating different fibres.
Another continent brings a different challenge. Our project with Bel Papyrus in Nigeria involves a combination of recycled fibre and virgin pulp. The customer required an entire deinking plant, with deinking cells, cleaning, screening, two-loop washing and hot dispersion, to guarantee the customer's required brightness. The project spans stock preparation to slitting/winding, including all engineering and procurement, electrification, control and ancillary items such as cranes, steam generation and sludge/water treatment.
Customer care is no longer shorthand for a spare parts service. We must be tissue making experts, at the customer's side until they achieve the tissue quality they seek. Customers need their supplier's help more than ever in order to produce saleable tissue with the minimum of downtime, possibly with challenging new fibres. An intimate understanding of refining, for example, is essential, plus comprehensive strategies to minimize fibre loss and the ability to stabilize the sheet and manage water retention, whatever the furnish.
Tissue machine developments.
While tissue machine suppliers have taken on the wider role of process supplier, the tissue machine itself cannot be neglected. Ask a tissue maker what their priorities are, and they are likely to cite bulk, runnability, ease of operation and, more than ever, energy saving. How do you square this with the fact that the traditional champion of bulk, TAD, is a big energy consumer? An option for the future is TAD with a serpentine design which has the potential to be less energy intensive than a traditional one or two drum solution. Watch this space.
Winding - the key to preserving bulk.
An important current option is to increase the bulk on a conventional machine and protect this with nip and torque control in winding, and this is why reel and then winder production has become such a critical area for us, in addition to the fact that the winding process is critical for retaining the stretch achieved by yankee creping and coating.
Toscotec's own range of winders and reels have been developed very much with the diversity of market needs in mind, with customization often the best solution. In China, for example, where Toscotec has a strong and growing reference list through Toscotec Asia & Pacific, our shaftless design is particularly appropriate.
More than just speed.
Outright speed in tissue production is no longer everything. Nobody wants to slow down, and we have recent references of 2,000 mpm lines in Europe, but productivity and efficiency are actually more important for the tissue maker's bottom line. Speed might seem the obvious way to increase productivity, minimizing downtime can have more impact. A good moisture profile will have more influence than outright speed, and the critical MWH/tonne energy consumption measure is not necessarily minimized by a relentless quest for more mpm.
This could be particularly important in China, where inland mills without a gas supply have to rely on coal for steam, but coal cannot achieve the capacity to dry a 2000 mpm sheet. Drying capacity is not the only issue. As more converters seek their own tissue making capacity, smaller, more energy efficient and easy-to-run tissue machines are frequently more appropriate than the widest, fastest units.
The common denominator is energy.
Throughout the world, energy is the big cost factor. In an existing set up, we need to advise how best to marry an efficient hood/yankee concept with the mill's energy supply and steam generation. In a greenfield scenario, we must design an energy-efficient heat and power generating solution to optimize the yankee and hood's performance. A recent Toscotec turnkey line in for MP Hygiene, France, which is very much focused on energy, features a two-press solution, steam generator and a cascade system for heat recovery on the hood, including turboblowers. This will become typical.
We have had to adapt and be more than just engineers. The tissue-making landscape has changed, and so have we.
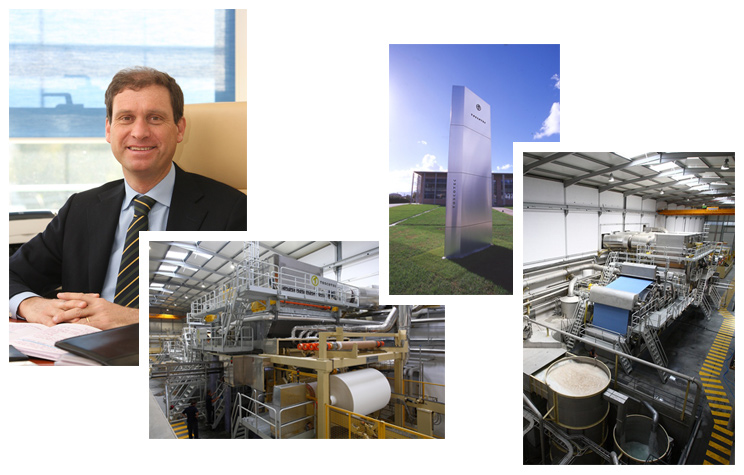
Back